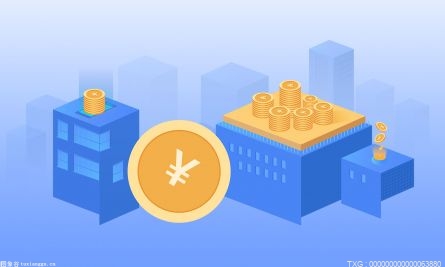
“充分挖掘降本空间”“把降本工作做到‘极致’”“每个环节、每个部门都要拿出明确的降本措施”……去年下半年以来,各部门、各生产单位深挖降本增效潜力、落实落细降本措施,自我加压、挑战极限,全力推动全流程降本增效。
今天,我们走进线材二分厂,看他们如何改进工艺,降低总脱碳层厚度,把降本增效不断推向深入。
(资料图片仅供参考)
受产品转移影响,线材二分厂B线主要生产规格由Φ5.5规格转变为Φ6.5规格。根据车间统计,发现2021年7月~2022年7月,Φ6.5规格脱碳层厚度超标次数占比较高。
脱碳现象是指钢材料在进行加热时表面的碳元素含量出现降低的现象。脱碳层超标会导致钢材料的硬度和强度下降,在进一步的机械加工过程中可能使加工出来的工件性能不达标。
为了降低Φ6.5规格总脱碳层厚度,改善产品质量,提高下游客户的满意度,线材二分厂迅速作出安排和部署,成立专项工作小组,全力推进降低Φ6.5规格冷镦钢和中高碳钢总脱碳层平均值。
首先,专项小组从实际出发,全面分析各工序、各环节影响总脱碳层厚度的因素,试图确定改进方向。“我们通过现场观察、论文查阅、逻辑推理等方法,梳理存在的问题,确定了加热温度、在炉时间、空燃比三个主要因素为改进方向。”线材二分厂轧钢工艺工程师蔡鹏说,瞄准改进方向,项目小组不断尝试,确定了几个投入成本低、可操作性强的提升对策。
经过讨论分析,项目团队将优化重点放在减少在炉时间上。加热炉是坯料轧制前加热的设备,被加热的钢坯从加热炉的装料端一步一步移送到出料端,并且使坯料在加热炉内达到所规定的温度。在不影响产量的前提下,专项小组提出将加热炉的装料方式由“满格装料”调整为“空格装料”,以此减少钢坯的在炉时间。
“经过头脑风暴,团队成员一致认可了这个方法,于是我们编制试验方案,并下发技术通知,组织安排试验。”蔡鹏说,在调整了装料方式以后,专项团队一开始比较担心82级中高碳钢的网碳合格率,但经过4-5次小批量的试验,并同步跟进金相检测数据和客户使用情况后发现,结果均合格,团队成员们这才放下心来。
此外,由于分厂冷镦钢牌号种类繁多、工艺复杂,产线上更换不同材质需要修改风冷线工艺参数,造成产线停车,在炉时间进一步增长。为此,专项小组还对风冷线工艺参数进行合并,来统一工艺参数、减少停车时间、提高生产效率。
与此同时,专项团队还通过校核加热炉热电偶准确性、优化控轧控冷工艺卡加热温度范围、调整残氧值检测方式和降低炉内残氧值等一系列改善措施,有效降低了Φ6.5规格产品总脱碳层厚度,在提高生产效率的同时降低了煤耗,预计节省20余万元/年。
YONGGANG
未来,线材二分厂将进一步苦练内功、挖潜增效,不断优化工艺,着力破解难题,争当降本增效“排头兵”。
关键词:
品牌